Handcrafted Leather Glasses Case: A Step-by-Step Guide
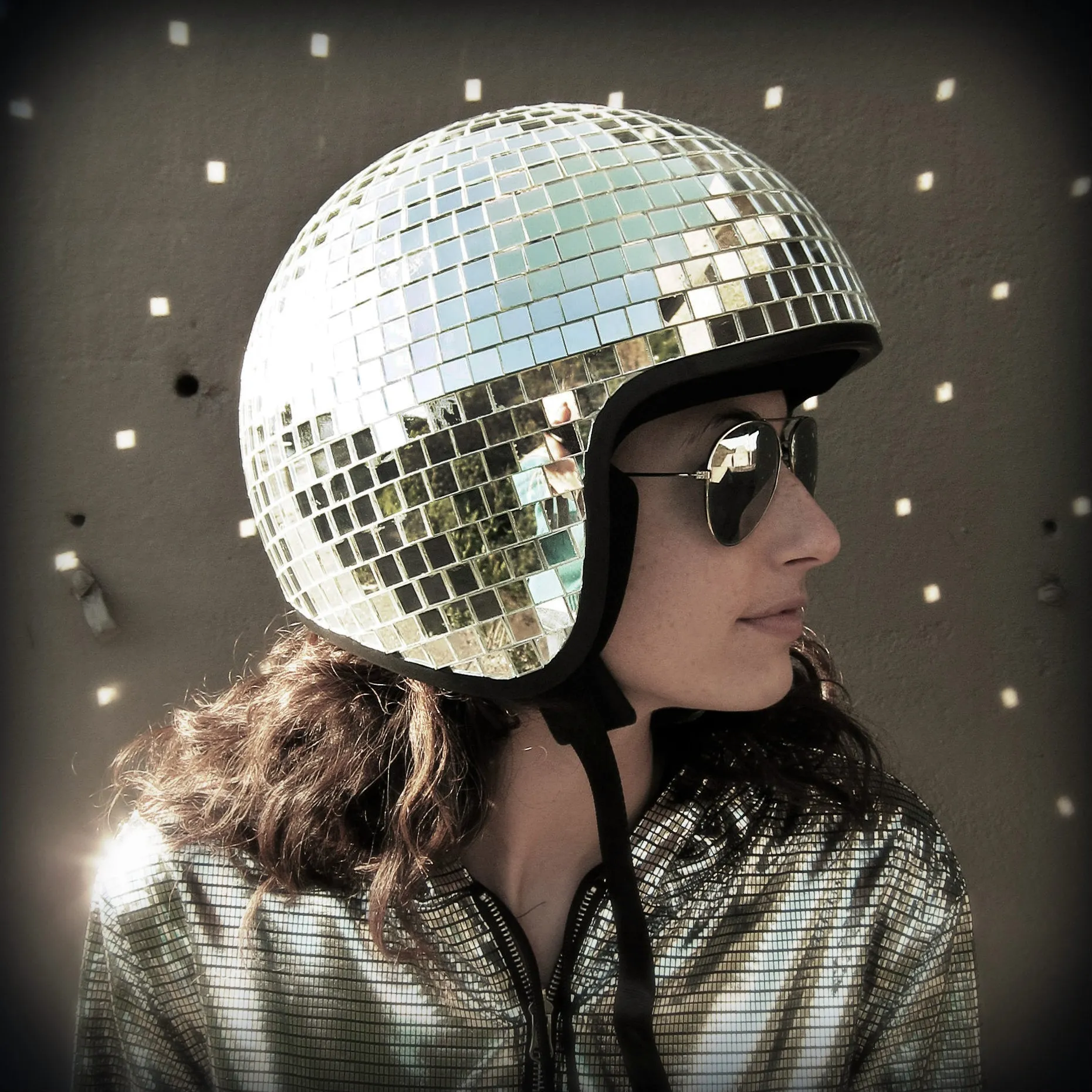
As someone who cherishes the art of handmade goods, I’m always drawn to the allure of leatherwork. There’s something inherently satisfying about transforming a simple piece of leather into something both beautiful and functional. This passion led me to explore the world of leather glasses cases – a project that perfectly blends practicality with artisanal charm.
This guide is a testament to that journey, offering a detailed walkthrough on how to craft your own handcrafted leather glasses case. Whether you’re a seasoned leatherworker or a curious beginner, join me as we delve into the intricacies of this rewarding craft.
Gathering Your Leatherworking Arsenal
Before we embark on our leatherworking adventure, let’s gather the tools and materials that will bring our vision to life:
Materials:
- Leather: Opt for a piece with a 4-5 oz thickness. This weight strikes a balance between durability and pliability, ideal for glasses cases.
- Dye: Unleash your creativity with an array of leather dyes. Experiment with different colors and finishes to achieve your desired aesthetic.
- Satin Leather Finish: This will be our trusty sealant, protecting the vibrant dyes and adding a touch of sophistication.
- Gum Tragacanth: This magical substance will be our secret weapon for burnishing the edges, lending a professional touch.
- One Line 20 Snap and Two Quick Set Rivets: These essential hardware components will ensure our case closes securely and elegantly.
- Wool Daubers and Sponges: These humble tools will prove invaluable for applying dyes, finishes, and gum tragacanth with precision.
Tools:
- Awl: A must-have for marking leather and creating precise holes.
- Sharp X-acto Knife: Our go-to for clean, accurate cuts.
- Adjustable Groover (Optional): While not mandatory, a groover helps achieve professional-looking stitching lines.
- Beveler (Optional): Like the groover, a beveler elevates the finesse of our edges, but it’s not essential for beginners.
- Hole Punches: For creating consistent and clean holes for rivets and snaps.
- Stitching Hole Punch (or Awl): Ensures evenly spaced holes for a polished stitch line.
- Wood Slicker: This will be our trusted companion for burnishing, adding a touch of professional polish.
- Waxed Thread and Needle: The backbone of our hand-stitched seams, adding a touch of handcrafted authenticity.
Natalina
Crafting the Blueprint: The Glasses Case Pattern
The foundation of our handcrafted masterpiece lies in a well-designed pattern. Start by researching different glasses case styles to find one that resonates with your taste.
Once you’ve found your muse, translate that inspiration into a tangible pattern. Use a sturdy piece of cardstock and a hard glasses case as your guide. As you refine your design, remember these tips:
- The Nose Bridge: Incorporate a bridge within the case to provide support for the nose of the glasses and the snap mechanism.
- Flap Length and Snap Placement: Fine-tune these elements to achieve both a secure closure and an aesthetically pleasing design.
Remember, this guide focuses on cases for reading glasses or slim sunglasses. If you’re crafting a case for larger frames, adjust the pattern accordingly.
From Pattern to Leather: Cutting and Marking
With our pattern finalized, it’s time to bring it to life in leather. Carefully trace the pattern onto your chosen leather using an awl, meticulously marking the locations for snaps, rivets, and stitching lines.
A sharp X-acto knife ensures clean cuts, preserving the integrity of your design. Remember to punch the holes for rivets using a 3mm punch for the case and a 4mm punch for the nose bridge. Save the hole for the front flap snap for last to guarantee a perfect fit.
Creating the Stitching Groove
An adjustable groover, while optional, elevates the craftsmanship of our case. This tool creates a subtle groove along the stitch line, allowing the stitches to sit flush against the leather. Maintain a consistent distance between the groove and the edge, as we’ll refine it further after stitching.
Precision in Every Stitch: Punching Stitching Holes
For a stitch line that exudes precision, utilize a 4-hole punch. For optimal consistency, try this technique:
- Align the tool with the last four holes punched.
- Punch only three new holes at a time.
This method, compared to eyeballing the spacing, leads to a more uniform stitch line. Don’t forget to include an extra hole in the middle section to secure the bottom edge when folded.
Refining the Edges with Beveling
A beveler, another optional tool, adds a touch of finesse to our leatherwork. Gently shave down the edges, excluding the area around the stitching, to create a subtly curved effect after burnishing.
Phoenix Mask
Adding a Personal Touch: Embellishment Options
This is where your creativity shines. Let’s explore two popular embellishment techniques:
1. Stamping:
Leather stamping allows you to imprint intricate designs onto your case. Here’s a step-by-step guide:
- Dampen the leather surface with a sponge.
- Position your chosen stamp – the possibilities are endless, from traditional patterns to found objects.
- Apply gentle pressure, even without a hammer, to create a lasting impression.
- Practice on a scrap piece to master the technique.
2. Laser Etching:
For a modern twist, laser etching opens up a world of intricate designs. This technique requires access to a laser cutter, but the results are striking:
- Conduct thorough tests on scrap leather to determine the ideal laser settings for your chosen design and leather type. Settings may vary significantly between designs and leather thicknesses.
- Once you’ve found your settings, proceed with etching your chosen pattern onto the leather.
Infusing Vibrancy: Applying Leather Dye
One of the most satisfying aspects of leatherworking is witnessing the transformation that occurs with dye. Using a sponge or wool dauber, apply the dye to your leather, experimenting with techniques like:
- Diluting: Create subtle washes of color by adding water to your dye.
- Layering: Gradually build depth and dimension by layering different dyes, blending quickly with a damp sponge to prevent harsh lines.
- Ombre Effects: Achieve a captivating gradient by concentrating a darker shade of dye along the edges.
Remember, leather dyes can react differently, so always test on a scrap piece to ensure your desired outcome.
Industrial End Tables
Securing the Structure: Setting Rivets and Snaps
With our case taking shape, it’s time to add the hardware that ensures its functionality:
Snaps:
- Gather your snap setting tool and a support for the curved side of the snap.
- Align the snap pieces, ensuring the leather lies flat, and hammer with the setting tool to secure them together.
- Remember to use corresponding snap pieces – one flat and one curved – to guarantee proper closure.
Rivets:
Adding the glasses support with rivets is a breeze:
- Align the rivet pieces through the designated holes.
- Place the rivet on a hard surface and hammer to set it in place.
The Art of the Stitch: Sewing the Case Together
The moment we’ve been building towards – uniting the pieces with a hand-stitched seam. Thread your needle with waxed thread and opt for a stitch that resonates with your style, be it a classic saddle stitch or a simple back-and-forth stitch. Tie off your threads securely, and admire the handcrafted character of your stitches.
Achieving a Polished Finish: Edge Preparation
For a professional-looking edge, trim any excess leather and utilize a beveler to create a smooth, refined edge along the newly stitched seam. Apply a thin coat of dye to the edges, preparing them for the burnishing process.
The Burnishing Touch: Achieving a Professional Sheen
Gum tragacanth, our secret weapon, takes center stage. Apply a light layer to the edges and, using your wood slicker, burnish the edges with back-and-forth motions. This creates a polished, glossy finish, elevating the overall craftsmanship of our case.
The Finishing Touch: Leather Finish
As a final act of care, apply a coat or two of leather finish to seal and protect our creation. This adds a layer of durability, ensuring our handcrafted case stands the test of time.
Fiber Optic Wings
A Handcrafted Legacy
Congratulations! You’ve successfully crafted a handcrafted leather glasses case – a testament to your creativity and leatherworking skills. This unique piece, imbued with your personal touch, makes a thoughtful gift or a cherished addition to your everyday essentials.
I encourage you to share your creations, insights, and leatherworking journeys. Leave a comment below – I’d love to hear from fellow artisans and enthusiasts. And if you’re looking for more handcrafted treasures, be sure to explore the exquisite collection on Robert Kline Art. Let’s continue to celebrate the beauty of handcrafted artistry together!