The Art of Washi Paper: A Timeless Tradition for Exquisite Gift Wrapping
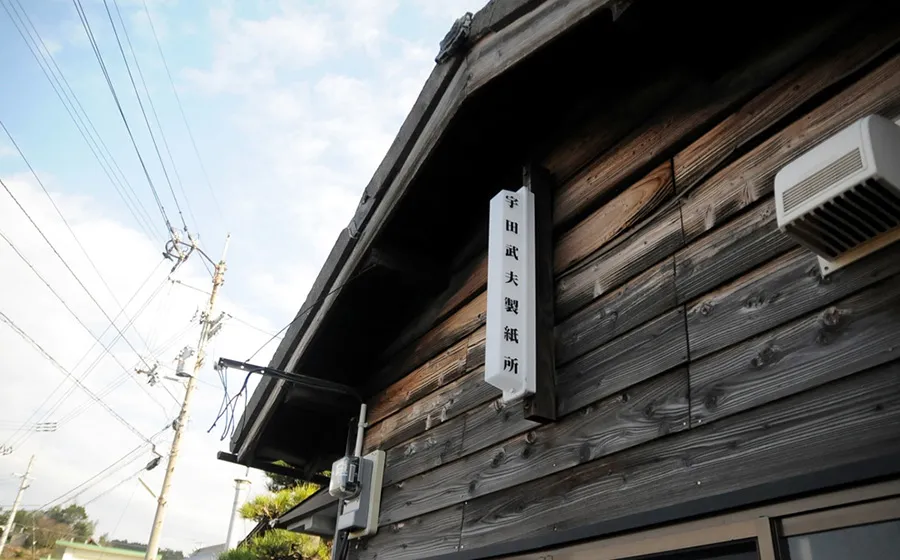
At Robert Kline Art, we believe that the beauty of a gift lies not just in its contents, but also in its presentation. There’s a certain magic in unwrapping a present that’s been thoughtfully and beautifully packaged, wouldn’t you agree? Today, we’re diving into the world of handmade washi paper, a traditional Japanese paper renowned for its elegance and unique texture, making it a perfect choice for elevating your gift wrapping game.
A Journey to Uda Paper Mill: Where Tradition Meets Passion
My fascination with washi paper led me to the doorsteps of Mr. Uda, a fourth-generation artisan and the heart and soul of Uda Paper Mill in Ehime prefecture, Japan. Stepping into his workshop was like entering a time capsule, a serene space where the gentle rhythm of water and the rhythmic sway of the Sugeta (bamboo papermaking tool) filled the air.
Outside of Uda Papermill (Photo by Yoko Takahashi)
The serene beauty of Uda Paper Mill, nestled in the heart of Ehime prefecture.
Mr. Uda’s dedication to his craft was mesmerizing. With meticulous care, he transformed raw fibers into exquisite sheets of washi paper, his practiced hands moving with a grace honed over 43 years. Every bubble meticulously removed, every imperfection swiftly addressed—a testament to the dedication ingrained in this ancient art.
Mr. Uda quickly removes bubbles created on the surface of the paper using a long straw (Photo by Yoko Takahashi)
Mr. Uda’s dedication shines through in his meticulous attention to detail.
“It’s just the perfect amount without feeling any pressure to finish more sheets,” Mr. Uda remarked as he crafted an average of 120-150 sheets a day. In a world obsessed with mass production, his commitment to quality over quantity is truly inspiring.
Today, Mr. Uda makes average 120-150 sheets a day. He says “it’s just the perfect amount without feeling any pressure to finish more sheets.”
Each sheet, a testament to Mr. Uda’s dedication and craftsmanship.
The Shrinking World of Handmade Washi Paper
The stark reality, however, is that artisans like Mr. Uda are becoming increasingly rare. The rise of machine-made paper, while efficient, has cast a shadow over traditional papermaking. During my visit, the sprawling factory floor, once abuzz with activity, stood as a reminder of the dwindling number of craftspeople keeping this heritage alive.
Yet, Mr. Uda persists. He continues to create over 20 varieties of washi paper, each one a testament to his artistry and a response to the dwindling number of clients seeking his craft.
Mr. Uda who has been making Washi papers for 43 years said at his humble manner, “I’m not a great master but I believe that I have made more variety styles of Washi papers than anyone else.”
Mr. Uda’s legacy: Preserving tradition through artistry and dedication.
Unveiling the Secrets of Washi Paper
Mr. Uda graciously walked me through the intricate process of crafting washi paper. It’s a process deeply intertwined with nature, relying on three primary materials: Kozo, Mitsumata, and Gampi.
Kozo, Gampi, and Mitsumata are the most popular materials for making Washi paper. They all have different characteristics.
Nature’s bounty: The raw materials behind the elegance of Washi paper.
Understanding the Three Musketeers of Washi Paper
-
Kozo: A member of the mulberry family, Kozo fibers are known for their strength and length. This makes Kozo paper remarkably durable and flexible, perfect for crafting items like Shoji screens and lamps.
-
Mitsumata: This shrub, related to the Daphne family, yields shorter, more delicate fibers. The result is a paper that’s luxuriously soft and smooth, ideal for high-quality stationery. Interestingly, Mitsumata paper is naturally insect-repellent, preserving calligraphy and artwork for generations.
-
Gampi: Falling between Kozo and Mitsumata in terms of fiber length, Gampi produces a paper that’s both strong and smooth, with a subtle sheen that exudes elegance. Like Mitsumata, Gampi paper also boasts natural insect-repelling properties.
From Bark to Beauty: The Making of Washi Paper
-
Preparation: The journey begins with soaking the barks, followed by a meticulous cleaning process to remove the outer layer. The fibers are then cooked in an alkaline solution, a crucial step in breaking down the material.
Cooking vat containing alkaline solution – Photo by Yoko Takahashi
The transformation begins: Cooking the fibers in an alkaline solution.Cooking vat with the top closed.
Sealing in the transformation: The cooking process in action. -
Cleaning and Refining: The cooked fibers undergo thorough washing to eliminate any residual alkaline solution. They are then meticulously cleaned to remove impurities – a process done by hand for the longer Kozo fibers.
"You see the fibers?” Mr. Uda showed me the raw material (prepared fibers) to make his Washi papers.
The essence of Washi: Cleaned and prepared fibers, ready for their transformation. -
The Art of Papermaking (Kamisuki): Now comes the heart of the process. The prepared fibers are mixed with water and neri, a natural thickening agent, to create a pulp. Using the Sugeta, Mr. Uda skillfully transforms this pulp into sheets, his movements dictating the paper’s thickness and texture.
With the desired thickness in mind, Mr. Uda moves his Sugeta back and forth. He carefully watches how the fibers are formed in the screen by balancing the amount of water and the fibers flowed in. (Photo by Yoko Takahashi)
The dance of creation: Mr. Uda masterfully shapes the pulp into sheets of Washi paper. -
Drying and Finishing: The freshly made sheets are carefully layered and left to dry overnight. While some modern mills use machines to speed up the process, Mr. Uda remains true to tradition, allowing his paper to air dry naturally on wooden panels, some of which have been in use for over 50 years!
Mr. Uda places his papers onto the flat wooden panels. “We have been using those panels over 50 years.” (Photo by Yoko Takahashi)
Timeless tradition: Air-drying on wooden panels, a testament to the enduring methods of Washi papermaking. -
Final Touches: Once dry, the sheets undergo a final inspection. With a keen eye, Mr. Uda uses a needle to remove any remaining imperfections, ensuring that each sheet meets his exacting standards.
Mr. Uda removes any dust or unwanted parts using the tip of the needle. (Photo by Yoko Takahashi)
A final touch of perfection: Mr. Uda ensures each sheet embodies the highest standards of Washi craftsmanship.
Elevating Gift Wrapping with the Soul of Washi
The laborious process and the meticulous attention to detail are what make handmade washi paper so special. It’s not just paper; it’s a work of art imbued with history, culture, and the artisan’s dedication.
“The feel of warmth, the subtle texture, the way it folds – washi paper brings an element of authenticity to gift wrapping,” says renowned gift wrapping expert [Expert Name] from [Expert Source/Company]. “It’s incredibly forgiving, making it perfect for even the most challenging shapes, and its durability allows you to achieve those crisp, professional edges.”
Gift wrapping design created with handmade Washi paper.
A gift that speaks volumes: The understated elegance of Washi paper elevates any present.
Embrace the Art of Washi
I encourage you to experience the magic of washi paper firsthand. Use it to wrap your next gift and witness how its simple elegance elevates your presentation. It’s a beautiful way to show your loved ones you care, adding a touch of handcrafted artistry to the occasion.
Looking to explore the art of gift wrapping further? Discover a world of techniques and inspiration at the Shiho Masuda Gift Wrapping Academy. Their online courses provide expert guidance to help you master the art of beautiful gift wrapping.
Let’s celebrate the tradition, artistry, and heart that goes into each sheet of washi paper, and embrace the art of gifting with intention and creativity!