Craft the Perfect Guitar Pedalboard: A Step-by-Step DIY Guide
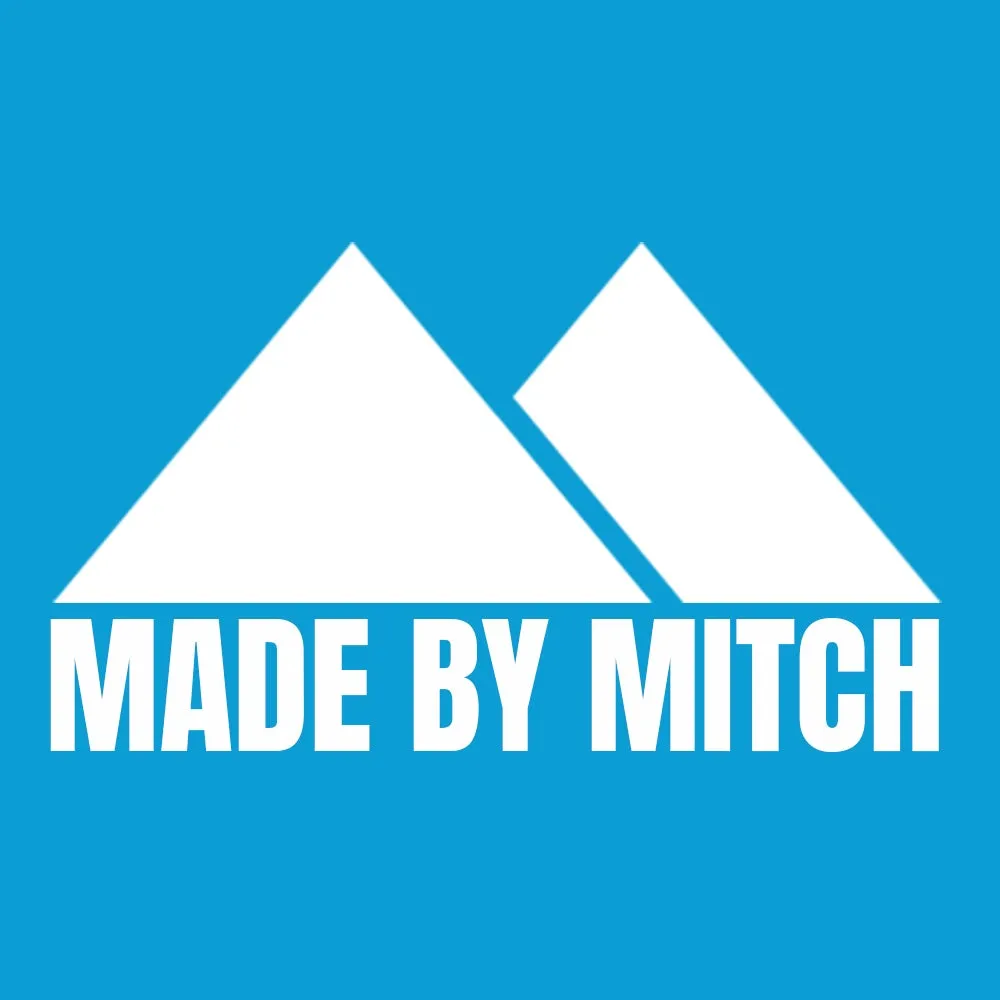
Hey there, fellow music lovers! Robert Kline, your friendly neighborhood art and craft aficionado, here. Today, we’re diving headfirst into the electrifying world of guitar effects with a DIY project that’ll make your heart sing – building a custom guitar pedalboard.
Madebymitch
Whether you’re a seasoned guitar hero or just starting your musical journey, a well-organized pedalboard can make all the difference. It’s the control center of your sonic universe, where raw sound transforms into musical magic. We’ll guide you through every step, from choosing the right materials to wiring your pedals like a pro. Get ready to unleash your creativity and craft a pedalboard that’s uniquely yours.
Planning Your Masterpiece: Size, Layout, and Design
Before we fire up the power tools, let’s take a moment to plan our sonic masterpiece.
1. Size Matters:
- Think about the number of pedals you want on your board.
- Measure your pedals to determine the overall dimensions.
- Remember to leave some breathing room for future additions!
2. The Art of Layout:
- Experiment with different pedal arrangements.
- Consider signal flow – typically, overdrive and distortion pedals go first, followed by modulation effects, and finally, time-based effects like delay and reverb.
- “I always recommend sketching out a few different layouts on paper before committing to one,” advises pedalboard guru, Sarah Jenkins. “It’s much easier to move things around on paper than it is to re-drill holes in your beautiful wooden creation.”
3. Design Your Dream Board:
- Will you go for a sleek and modern look or a more rustic, handcrafted vibe?
- Consider the materials – wood, metal, even acrylic can be used.
- “Don’t be afraid to let your personality shine through,” encourages Sarah. “A custom pedalboard is an extension of your musical voice.”
Tools and Materials: Gathering Your Sonic Arsenal
Now that you’ve got a vision, let’s gather the tools and materials to make it a reality. You’ll need:
Woodworking Essentials:
- Wood: Walnut, oak, and cherry are popular choices for their durability and beauty.
- Plywood: For the top and bottom of the pedalboard.
- Wood Glue: To create strong, lasting joints.
- Danish Oil and Polyurethane: To protect and enhance the wood’s natural beauty.
- Sandpaper: For smoothing out rough edges and preparing the wood for finishing.
- Circular Saw, Table Saw, Jigsaw: For cutting the wood to size.
- Drill and Forstner Bits: For drilling holes for mounting pedals and electronics.
- Router: For creating rounded edges and recesses for electronics.
- Clamps: To hold pieces together while the glue dries.
Electronic Components:
- Pedalboard Power Supply: To power your pedals safely and efficiently.
- Audio Jacks: For input and output connections.
- DC Power Jack: For connecting the power supply.
- Wiring: To connect all the electronic components.
- Soldering Iron and Solder: For making secure electrical connections.
Finishing Touches:
- Pedalboard Carpet: Provides a non-slip surface for your pedals.
- Velcro: For attaching pedals to the carpet.
- Rubber Feet: To protect the bottom of your pedalboard and prevent it from scratching surfaces.
Building Your Pedalboard: From Raw Materials to Rock ‘n’ Roll
1. Mill the Lumber:
- Start by milling the wood to your desired thickness and width.
- If you don’t have access to woodworking tools, many lumber yards can mill the wood for you.
2. Shape and Join the Sides:
- Cut the sides of the pedalboard to size and create the desired taper if you’re going for a slanted design.
- Use a joinery method like box joints, mitered corners, or butt joints to connect the sides together.
3. Create the Top and Bottom:
- Cut the plywood to size for the top and bottom of the pedalboard.
- Attach the top to the sides using wood glue and screws.
- Before attaching the bottom, you’ll need to cut out recesses for the electronics.
4. Install the Electronics:
- Mount the power supply, audio jacks, and DC power jack to the bottom of the pedalboard.
- Drill holes for the wiring to pass through.
- Wire the components together according to the power supply’s instructions.
- “Always double-check your wiring before plugging anything in,” cautions Sarah. “A short circuit can damage your pedals and even be dangerous.”
5. Sand and Finish:
- Sand the entire pedalboard smooth, starting with a coarser grit sandpaper and gradually moving to finer grits.
- Apply several coats of Danish oil, allowing each coat to dry thoroughly before applying the next.
- Follow with a few coats of polyurethane for a durable and water-resistant finish.
6. Attach the Carpet and Rubber Feet:
- Cut the pedalboard carpet to size and adhere it to the top of the pedalboard using spray adhesive.
- Attach rubber feet to the bottom corners of the pedalboard to protect surfaces and provide stability.
7. Add the Finishing Touches:
- Install a handle on the front or side of the pedalboard for easy transport.
- Consider adding a hinged lid to protect your pedals and wiring during transport.
Congratulations! You’re Ready to Rock!
You’ve done it! You’ve transformed raw materials into a custom guitar pedalboard that’s ready to unleash your sonic fury. Now it’s time to wire up your pedals, plug in your guitar, and let your musical creativity soar. Remember to share pictures of your creations in the comments below!
Looking for More Creative Inspiration?
Discover a world of unique, handcrafted gifts and DIY projects at [Robert Kline Art](your website link). From handmade jewelry to custom artwork, we have something special for every occasion. Let us help you find the perfect gift or inspire your next artistic endeavor!